Description
The SK2 series vacuum tube-type high temperature sintering furnace integrates the control system and the furnace chamber. The furnace lining uses vacuum formed high-purity alumina ceramic fiber material, and uses resistance wire / silicon carbide rod / silicon molybdenum rod as the heating element. The furnace tube traverses the middle of the furnace body as the furnace chamber. The two ends of the furnace tube are sealed with stainless steel flanges. The workpiece sample is heated in the furnace tube. The heating element is parallel to the furnace tube and is evenly distributed outside the furnace tube to effectively ensure the uniformity of the temperature field. Thermocouples (K/S/B type) with stable performance and long service life are used for temperature measurement to improve the accuracy of temperature control. It is a special equipment specially developed for the sintering, melting and analysis of metals, non-metals and other compound materials in the atmosphere or vacuum state by universities, scientific research institutes and industrial and mining enterprises.
The control panel of the furnace body has an intelligent temperature regulator, which controls the power switch, the main heating work/stop button, and is equipped with power and insurance indicator lights, voltage and current instructions, so as to observe the working status of the system at any time.
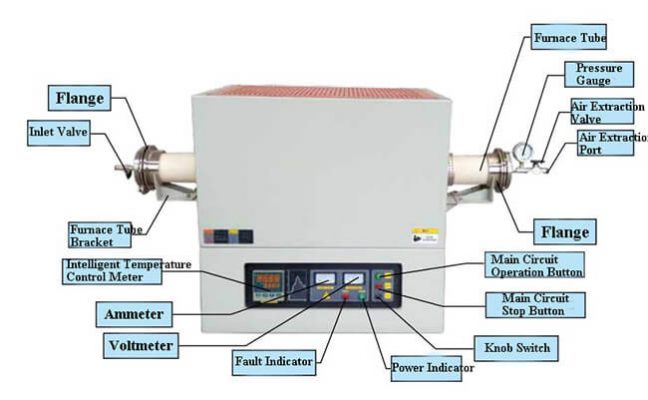
Product Application
Tube-type furnaces are mainly used in metallurgy, glass, heat treatment, lithium battery positive and negative materials, new energy, abrasive tools and other industries, and are professional equipment for measuring materials under certain temperature conditions. This furnace has simple structure, and is easy to operate and control, and capable of continuous production.
Product Advantages
SK2 series (1200℃ /1400℃ /1700℃) tube-type furnace has the following advantages:
- 30-segment intelligent temperature control regulator, PID control, temperature control accuracy ±1 degree.
- The temperature upper limit alarm can be set, and the main circuit can be automatically cut off when the temperature exceeds the upper limit.
- High-purity alumina ceramic fiber is used as the furnace chamber material, which has good thermal insulation effect. The furnace tube can be quartz tube / stainless steel tube / corundum tube according to the temperature.
- Single temperature zone, double temperature zone, three temperature zone and five temperature zone can be customized according to customer requirements.
- Using KF flange, which has good sealing performance and high vacuum.
- With RS232 interface, it can communicate with computer (optional).
Product Features
Product Usage | It is widely used in scientific research and small batch production of enterprises and institutions, as well as ceramics, metallurgy, electronics, glass, chemical industry, machinery, refractory materials, new material development, special materials, and building materials involved in scientific research and teaching in colleges and universities. | ||
Temperature | 1200℃ | 1400℃ | 1700℃ |
Temperature control accuracy | ±1℃ | ±1℃ | ±1℃ |
Thermocouple and measuring range | K type(0-1200℃) | S type(0-1600℃) | B type(0-1820℃) |
Heating element | Resistance wire | Silicon carbide rod | Silicon molybdenum rod |
Exterior design | The electric furnace adopts humanized design, has beautiful appearance, simple operation, and the outer paint layer uses a high-temperature baking process with plastic spraying. It has high temperature resistance, oxidation resistance, acid and alkali resistance. The color is chosen to be resistant to aging, and the appearance of the color will not fade due to long use. | ||
Shell design | The shell of electric furnace adopts a double-layer forced air-cooling structure, so that the outer temperature of the furnace shell is close to room temperature when the electric furnace is working at the highest temperature, avoiding accidental damage. | ||
Temperature control method | Adopt the most advanced temperature controller in the world: with 30-51 section programmable PID self-tuning, automatic heating, automatic cooling, no need to be on duty. RS-485 communication interface is also optional (connect to an ordinary computer to start, stop, pause heating, set heating curve, heating curve storage, historical curve records, etc.) | ||
Temperature control safety | The electric furnace adopts coking circuit, module control, and dual-circuit protection (bias temperature protection, ultra-high temperature protection, broken couple protection, overcurrent protection, overvoltage protection and other protection functions) to make the electric furnace work stable, reliable and safe. | ||
Heating rate | The maximum heating rate is 30°C/min, and 20°C/min is recommended. | ||
Material of furnace chamber | Using the most advanced light alumina ceramic fiber in the world, it has excellent heat preservation effect, light weight, high temperature resistance, rapid cold and rapid heat resistance, no cracks, no crystallization, no slag, and no need to worry about pollution to the fired product. The energy saving effect is 60%-80% of the old electric stove. | ||
Design of furnace chamber | The furnace chamber adopts a stepped assembly structure and incorporates the laws of mechanics, which effectively guarantees the uniform force of the furnace chamber during the heating process, ensures that the heat energy is not easily lost, and prolongs the service life of the furnace chamber. | ||
Passable gas | All inert gases, mixed gases, nitrogen, carbon dioxide, water vapor, hydrogen, and oxygen… | ||
Gas control | The air inlet can be provided with one or more air inlets, and each air inlet is provided with a needle valve connected to a vacuum gauge. The air outlet is connected with an air outlet, and all holes are equipped with needle valves. Equipped with a vacuum pump. | ||
Sealing method | The 304 stainless steel flange is used, which is easy to install and unload, anti-oxidation, anti-acid and alkali, and double-layer sealing to ensure the tightness. | ||
Warranty period | The electric furnace has a free warranty of 12 months (except for the heating element), and the heating element and cooling fan that are naturally damaged within 3 months are free to be replaced. | ||
Accessories | Standard accessories: one vacuum pump, one crucible tongs, one pair of special high-temperature gloves, one instruction manual.
Optional accessories: touch screen control, paperless recorder, remote communication control system. |
||
Product certification | EU standard CE certification ISO 9001:2008 quality management system certification. |
Product Parameters
一、1200℃ tube-type furnace
Model | Highest temperature(℃) | Chamber size(mm) | Input power/power(V/KW) |
SK2-2-12TPA2 | 1200℃ | Φ40×205 | 220V/2KW |
SK2-3-12TPB2 | 1200℃ | Φ60×205 | 220V/3KW |
SK2-5-12TPC2 | 1200℃ | Φ80×205 | 220V/5KW |
SK2-5-12TPD2 | 1200℃ | Φ100×205 | 220V/5KW |
SK2-3-12TPA3 | 1200℃ | Φ40×350 | 220V/3KW |
SK2-4-12TPB3 | 1200℃ | Φ60×350 | 220V/4KW |
SK2-5-12TPC3 | 1200℃ | Φ80×350 | 220V/5KW |
SK2-6-12TPD3 | 1200℃ | Φ100×350 | 220V/6KW |
SK2-4-12TPA4 | 1200℃ | Φ40×440 | 220V/4KW |
SK2-4-12TPB4 | 1200℃ | Φ60×440 | 220V/4KW |
SK2-6-12TPC4 | 1200℃ | Φ80×440 | 220V/6KW |
SK2-7-12TPD4 | 1200℃ | Φ100×440 | 220V/7KW |
二、1400℃ tube-type furnace
Model | Highest temperature(℃) | Chamber size(mm) | Input power/power(V/KW) |
SK2-2-14TPA2 | 1400℃ | Φ40×205 | 220V/2KW |
SK2-4-14TPB2 | 1400℃ | Φ60×205 | 220V/4KW |
SK2-5-14TPC2 | 1400℃ | Φ80×205 | 380V/5KW |
SK2-6-14TPD2 | 1400℃ | Φ100×205 | 380V/6KW |
SK2-3-14TPA3 | 1400℃ | Φ40×350 | 220V/3KW |
SK2-5-14TPB3 | 1400℃ | Φ60×350 | 220V/5KW |
SK2-6-14TPC3 | 1400℃ | Φ80×350 | 380V/6KW |
SK2-7-14TPD3 | 1400℃ | Φ100×350 | 380V/7KW |
SK2-4-14TPA4 | 1400℃ | Φ40×440 | 220V/4KW |
SK2-5-14TPB4 | 1400℃ | Φ60×440 | 220V/5KW |
SK2-7-14TPC4 | 1400℃ | Φ80×440 | 380V/7KW |
SK2-8-14TPD4 | 1400℃ | Φ100×440 | 380V/8KW |
三、1700℃ tube-type furnace
Model | Highest temperature(℃) | Chamber size(mm) | Input power/power(V/KW) |
SK2-3-17TPA2 | 1700℃ | Φ40×205 | 220V/3KW |
SK2-4-17TPB2 | 1700℃ | Φ60×205 | 220V/4KW |
SK2-6-17TPC2 | 1700℃ | Φ80×205 | 380V/6KW |
SK2-7-17TPD2 | 1700℃ | Φ100×205 | 380V/7KW |
SK2-4-17TPA3 | 1700℃ | Φ40×350 | 220V/4KW |
SK2-5-17TPB3 | 1700℃ | Φ60×350 | 220V/5KW |
SK2-7-17TPC3 | 1700℃ | Φ80×350 | 380V/7KW |
SK2-8-17TPD3 | 1700℃ | Φ100×350 | 380V/8KW |
SK2-5-17TPA4 | 1700℃ | Φ40×440 | 220V/5KW |
SK2-6-17TPB4 | 1700℃ | Φ60×440 | 220V/6KW |
SK2-9-17TPC4 | 1700℃ | Φ80×440 | 380V/9KW |
SK2-10-17TPD4 | 1700℃ | Φ100×440 | 380V/10KW |
Maintenance Considerations
- After the furnace is used for the first time or not used for a long time, it should be baked at about 120℃ for 1 hour, and used at about 300℃ for 2 hours to avoid cracking the furnacechamber. The furnace temperature should not exceed the rated temperature to avoid damage to the heating element and furnace lining. It is forbidden to directly pour various liquids and dissolved metals into the furnace chamber to keep the furnace clean.
- If the corundum furnace tube is used in the furnacechamber, according to the physical properties of the corundum material, the temperature rise and fall rate of each temperature zone should not be too fast (≤5℃), and it is strictly forbidden to take the material above 100℃ in the furnace tube. It is conducive to the uniform release of the thermal stress of the furnace tube to extend the service life of the furnace tube.
- If the furnace body uses silicon-molybdenum rods as heating elements, according to the physical characteristics of silicon-molybdenum rods, it is very brittle at room temperature. Therefore, the furnace body cannot be disassembled and moved at will after the heating elements are installed. It is not advisable to run for a long time in the temperature range of 400-700℃, otherwise the silicon molybdenum rod will undergo low-temperature oxidation, which will cause component damage.
- If the furnace body uses silicon carbide rods as heating elements, the resistance will gradually increase after long-term operation. This phenomenon is called “aging”. After the furnace has been running for a period of time, due to the aging of the silicon carbide rods, the heating rate and ideal temperature of the furnace will not reach the original values. Please adjust the OPH value appropriately and observe that the main current of the ammeter is at an appropriate level. When individual components are damaged due to some reasons and need to be replaced, the components with suitable resistance value should be selected according to the increase of the resistance value of other original components at that time, and new components cannot be replaced at will. If the components are damaged or the resistance value increases too much, it is best to replace them with new components when the required furnace temperature cannot be reached.
- When the cold furnace is used, since the furnace chamber is cold and must absorb a lot of heat, the temperature rise rate in the low temperature section is not easy to be too fast, and the difference in the temperature rise rate of each temperature section is not too large. When setting the temperature rise rate, full consideration should be given to the physicochemical property of the sintered material, so as to avoid the phenomenon of spraying and polluting the furnace tube.
- Regularly check whether the electrical connection part of the temperature control system is in good contact, and special attention should be paid to whether the connection of each connection point of the heating element is tight.
- After the furnace has been used for a period of time, if the vacuum level decreases, the temperature-resistant silicone ring between the stainless steel flanges can be replaced or the stainless steel flanges can be reinstalled or the vacuum system can be replaced and repaired to improve the overall vacuum of the system.
- The temperature of the furnace is generally around 300℃ during the working process. If the control deviation cannot be eliminated, the temperature display value does not match the program setting value or the swing is too large, please check whether the parameter “M5, P, t” is set accurately.
- Using B-type high temperature dual platinum rhodium (30%-6%) thermocouple, the measuring accuracy of the meter is 0.5 grade at 0-600℃, and 0.2 grade can be guaranteed at 600-1700℃. The measurement accuracy of S-type single platinum rhodium thermocouple can be guaranteed to 0.2grade.
- This furnace is suitable for the following working conditions:
(1) The ambient temperature is between -10 and 75℃.
(2) The relative humidity of the surrounding environment does not exceed 85%.
(3) There is no conductive dust, explosive gas or corrosive gas that can seriously damage metals and insulating materials around the furnace.
(4) There is no obvious tilt, vibration and bumps.
- If the actual control of each furnace body does not match the picture in the manual, the actual product shall prevail, but the control operation method is the same.
Common Faults and Solutions
Failures | Causes | Solutions |
Turn on the control power switch LOCK, but no power indication | The fuse of control line FU1 is broken | Check whether there is short circuit, and replace the fuse after elimination |
Meter SV alternately displays Oral | Thermocouple breaks | Replace the thermocouple |
Meter SV alternately displays HIAL | The furnace body exceeds the upper limit temperature | When the temperature drops to the safe temperature, the meter automatically returns to normal (check the cause of overtemperature) |
The power supply is normal but the furnace body is not working | Meter parameters are incorrectly modified | Change to the correct parameter |
Power supply and heating elements are normal, but the furnace body can not heat up | The control circuit is damaged | Inform professional maintenance personnel |
The temperature displayed by the meter is not consistent with the temperature of the lofting area, resulting in positive or negative deviation | The deviation of the temperature measurement point and the position of the stakeout point, or the deviation of the resistance value of the heating element in the microscopic view, is a normal phenomenon | Correct the lofting position, or notify the maintenance personnel to manually correct |
Matching Products
1、Crucible tong
2、High temperature gloves
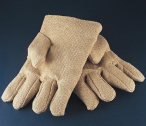
3、Vacuum pump
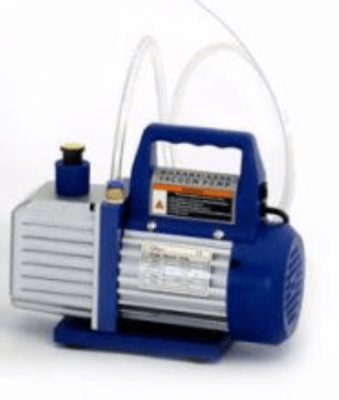
Packing and Delivery
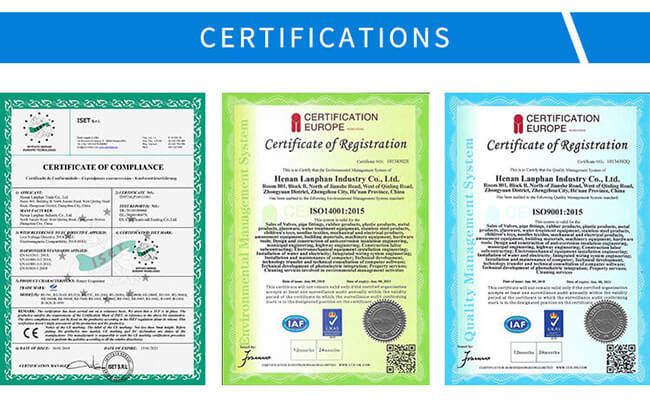
Pre-Sale Service
- Provide 24-hour technical consultation and reply;
- Provide professional quotation information;
- Provide detailed product performance specification;
- According to product’s using condition, technicians will offer rationalization proposals to assist clients to select proper product types;
- Provide other corollary equipment according to client requirements.
In-Sale Service
- With supervision from the source of products, the qualified rate of raw materials entering the factory can reach 100%;
- Whole manufacturing process are in strict accordance with promised procedure requirements, product qualified rate can reach100%;
- Provide product’s inspection record of key junctures to customers;
- Provide production schedule photos to customers at regular intervals;
- Package and transport of products are in strictaccordance with the export standard;
- Provide transportation schedule information to clients timely.
After-Sale Service
- Provide targeted installation video;
- Under the premise of correct installation, normal maintenance and using, we guarantee one-year warranty period;
- When warranty period has expired, our sold products enjoys lifetime guarantee repair, we only charge cost price for changing product’s standard component and sealing component;
- During installation and adjustment period, our after-sale service staff will communicate with customers frequently to know product’s running state in time. Assist customers to install and adjust products until customers are satisfied;
- If product has malfunction during operation period, we’ll offer you satisfied answer in time. We’ll reply you within 1 hour and provide solution or send staff to spot within 24 hours after receiving maintenance notification;
- Lifelong free technical support. Conduct satisfaction survey and inquiry equipment running condition to clients by telephone or e-mail semiannually from the first day of equipment running, put on records of acquired information;
- Provide assistance in solving problems such as equipment damage in the transport.
Reviews
There are no reviews yet.